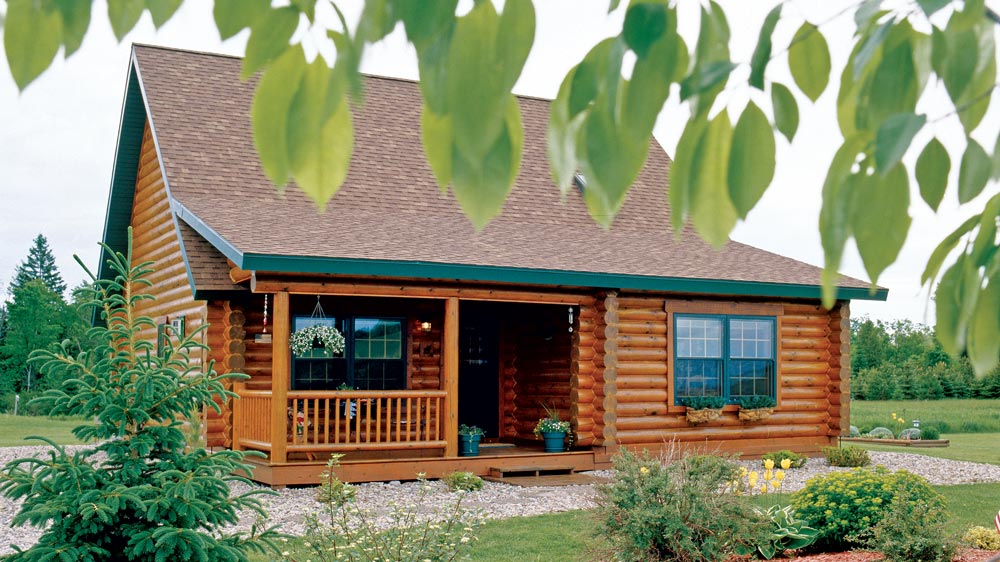
Photo: Roger Wade / Home: Hiawatha Log Homes
As a builder, I’m not just a guy that assembles houses; I’m also an advisor. The first thing I make sure my clients understand is that a full-scale, custom log or timber home will cost more than a conventional stick-framed house. It’s simply the reality. This is largely due to the quality of the materials and craftsmanship that go into log and timber homes. Plus, the more remote your location, the more infrastructure essentials (like access roads, foundation, electricity, water, etc.) can drive up costs — fees that are not negotiable or within your control.
But don’t panic. After those hard costs are covered, there are many tactics you can take to keep your budget in check and get the log or timber home you’ve been longing for. In my experience, these five strategies will make the biggest impact: 1. Downsize and Simplify.
As a general rule, the more square or rectangular you can keep a log or timber home, the less expensive it becomes.
To lower costs, only include spaces and features that are needed. Scrutinize each room within the design and ask yourself if you can make it smaller while keeping it livable. Look for ways to reduce the overall footprint (which will save money on foundation costs) and then, if needed, increase square footage by going vertical (the more spread out a house is, the more expensive it becomes). Just understand that there will be other concessions/costs, for materials and labor to construct the upper level.
2. Choose Wood Wisely.
In the log and timber home industry, wood comes in a variety of sizes and species, and both play a big part in your budget. Some are more expensive than others (for example, a 6-inch log will cost less than an 8-inch of the same species; white pine costs less than Douglas fir), so it pays to shop your options. However, always start with what is recommended in the region where you’ll be building. From there, selections like complex truss systems, exposed rafters, accent timbers, carvings, etc., all cost more.
To save a little cash without sacrificing the beauty of the wood, be strategic in how and where you use it.
For a log home, keep the full logs to the perimeter walls and opt for an enclosed roof-rafter system (framed with conventional wood studs). If you want interior log walls, select half-log siding, which can save some money while maintaining the log home look.
In a timber frame, keep the truss style simple and straightforward, and design the house on the smaller side to reduce the number of bents (timber segments) required. Or, only use the timber frame in the main core of the home and go with conventional materials for the wings.

Plans: Hiawatha Log Homes
3. Minimize Labor Costs.
It’s no secret that there’s a shortage of builders in this country, and as a result, labor costs have risen. If you’re building in a market where labor charges are extraordinarily high, like northeast New York, for example, you may assume there’s no way around it, but there is. Using building systems and prefabricated components, like trusses and interior wall panels, reduce the time builders spend constructing the house on the job site, saving you money and enabling your home to be completed more quickly, which may also save you a few interest payments on your construction loan.
4. Select Frugal Finishes.
One way I convey the concept of size versus cost to my clients is to give them a “Christmas gift” analogy, and it goes like this: There are two gifts under your Christmas tree. One box is huge; the other is tiny. Both are beautifully wrapped. When you open the big one, it’s filled with practical items like a wool blanket, socks and a sweater. Inside the tiny one is a diamond tennis bracelet. The large box is worth about $200, while the small one is worth $2,000 — the value all depends on what’s inside the box, not its size.
5. Shop Smart, Shop Early.
We all want the latest, greatest thing. It’s in our nature. So how do we balance this craving with our desire to follow tip #4? By following tip #5.
The time to start shopping for your home’s finishing materials is not once your home is weather tight and the contractors are ready for cabinets, sinks and flooring; it’s when you finalize your construction documents. At this point, you’ll know exactly the kind and quantity of everything your home needs, from light fixtures to outlet covers; so when you find items on sale, buy them! Rent a storage unit to stow your finds and keep it on the job site so items will be handy when the crew needs them. The last thing you want to do is order materials when the builder asks for them – delivery lags will throw your construction schedule off, which may also add unnecessary fees. And purchasing items along the way will help spread out the cumulative cost, making it easier to digest.
but I can think of no better way to spend it than to fulfill your log or timber home dream.