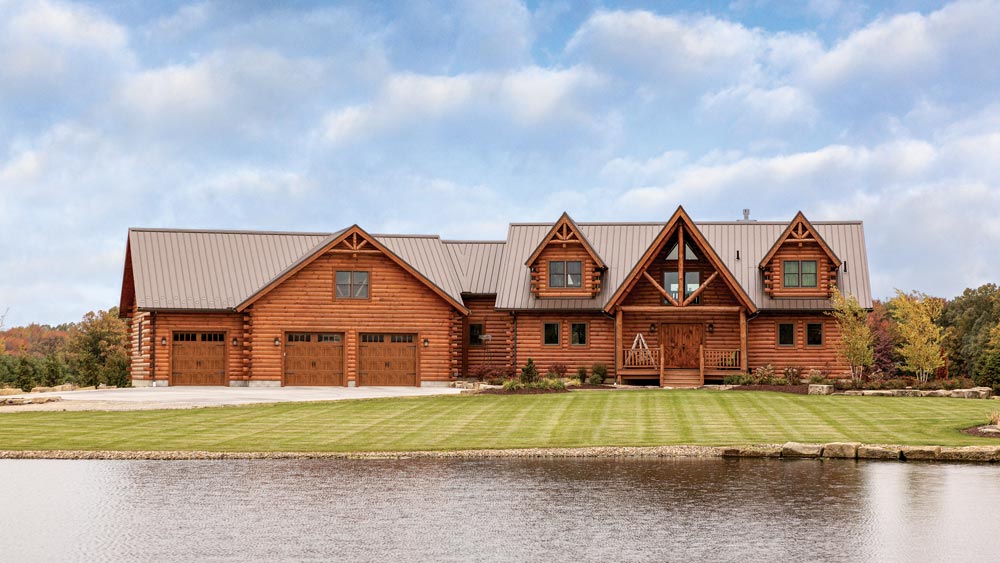
Log homes are arguably the most recognizable type of residential construction in the world. While it takes a fairly trained eye to discern the difference between a Georgian Revival and a Queen Anne manse, you don’t have to have a degree in architectural design to know in an instant — that’s a log home!
But even in the log home realm, there are nuances that may not be easy to spot, unless you know what you’re looking for. This starts with identifying the distinct features of a milled log home.
What is a milled log home?
Unless you’re living in the Rocky Mountain region or the Canadian wilderness, most of the log homes you see are milled. In fact, milled log home producers make up roughly 90 percent of the industry.
To craft their homes, manufacturers use computerized saws and planers to shape the trees to uniform sizes — but don’t mistake this conformity for a lack of originality. Though the logs are precision-cut, there are a variety of shapes and styles from which to choose, including round, rectangular, beveled or D-shape (flat on one side, round on the other). And the choices don’t stop there. The corners can be joined with a dovetail (for squared logs), saddle-notch (for round logs), butt-and-pass (where one log ends at a cross member that passes it), or corner post (where all logs dead end into a vertical “cap”) system. The combination of these options makes for a highly customized log home.
Why does milled matter?
Well, for starters, milled logs are usually less expensive thanks to the speed and precision of the machinery used to debark and cut them to the specified shape (profile). The raw timbers, themselves, are often narrower (typically less than 12 inches in diameter), and depending on the chosen species, this can help to reduce the price at the onset.
Cost isn’t the only consideration, however. The milling process also affects the look of the home. Milled logs are commonly cut to the exact same width and length at the butt ends and are sanded to a smooth texture, giving the home a very uniform appearance — a trait that appeals to buyers who seek symmetry.
Settling is another key contributing factor to the process. Wood shrinks and settles as it dries, but milled-log home manufacturers start with very dry wood to keep settling to a minimum. (By contrast, handcrafted logs typically have a higher moisture content and, thereby, result in greater settlement in a stacked wall.)
The exactness of the milling process also can impact the tightness of the logs where they intersect. For example, a milled log can be cut with a tongue-and-groove profile, which enables the logs to literally lock together. When combined with foam gaskets, this option makes for a very tight seal. Chinking (the elastic material used to fill gaps between handcrafted logs) isn’t necessary here, but can be applied as an additional sealant or even just for aesthetics.
Speed of construction may be the best benefit. It will take a crew about two to three days to erect a 2,500-square-foot milled-log shell. Though it will still take several months to finish the house and obtain a certificate of occupancy, this speedy building system allows buyers near-instant gratification, as the process goes from empty lot to defined dream home in a snap.