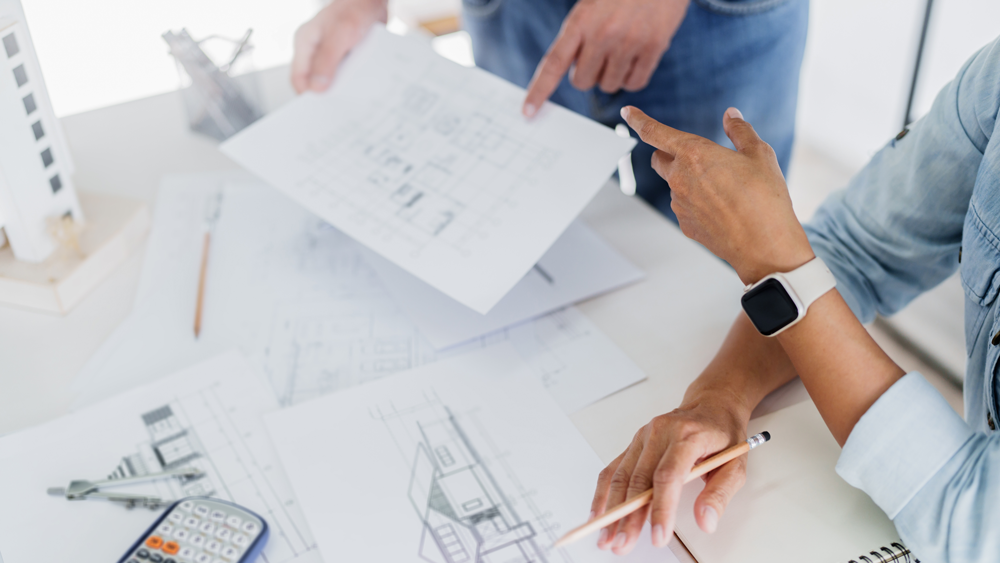
You’ve purchased land. You’ve got your floor plans and engineered construction docs in hand. Your builder is on board. The time has finally come — you’re ready to build that log or timber frame home you’ve been planning for months, years … maybe most of your life. With so much invested, both financially and emotionally, of course you want it to go off without a hitch.
The fact is that almost every construction project experiences a delay at some point in the process. The sooner you accept that fact, the less stressful it will be. That said, there are some things you can do to mitigate or even prevent common interruptions to the construction schedule. These are five of the most frequent causes of delay that I’ve seen in my 30-plus years as a custom log and timber home builder. More importantly, here’s how to avoid them.
Cause of Delay: PERMITS
Often people assume that because the plans are drawn and engineered, their financing is in place and their builder is hired, they’re ready to start construction. But what they don’t realize is that once they decide to pull the trigger, the builder has to pull the permit. Depending on the municipality, it can take weeks and even months to receive approval and start construction, because those plans must be thoroughly reviewed and deemed compliant with the area’s building codes.
How to Avoid It:
To start, make sure you have a everything your local permitting office needs for its review, including a complete set of construction documents. Depending on how much construction activity is occurring in your area, it can take some time for your application to make it to the top of the queue, which is time consuming enough. But the minute your application is found to be incomplete or have an error, the permitting official will immediately stop the review and kick the plan back to you. Then, once the issue is rectified, your builder will need to resubmit … and you’ll be at the back of the line again. The permitting office isn’t trying to punish you. It’s necessary because each element has an impact on the rest of construction, so if something in the plan is missing or non-compliant, there’s no need to look at the rest of it.
How do you know if yours is ready to formally submit? Many permitting offices have what’s called a “pre-plan review” process, in which a contractor and permitting officer review the plan together to ensure it meets the criteria, or, if not, note the errors for correction before it’s formally submitted. The more complete and accurate the drawings are, the faster you’ll get those permits.
Cause of Delay: WEATHER
In construction, dealing with the weather is always a concern. Despite a contractor’s best efforts, it almost always gets in the way at some point during a build.
How to Avoid It:
There may not be a whole lot you can do to fight Mother Nature, but you can do your best to outsmart her by starting construction at the most opportune time of the year in the area where your home will be built. For much of the United States, that time is spring, once the last hard frost has passed, or after the rainy season has subsided. Can homes be started in the middle of winter? Sure. But the farther north you go, the smaller that window gets and the more potential you’ll have for weather-related delays. In the South, you have a wider building span, but you do have to work around hurricane season. In areas like the Rockies, it can be balmy one day and snowy the next, throwing your builder’s schedule a curveball.
The good news is that when you’re working with logs and timbers, you can get what we in the building industry call “in the dry” fast, meaning the shell is up, the roof is on and tasks like mechanicals, flooring and cabinetry installation can proceed inside without nature’s interference.
Cause of Delay: STRUCTURAL ALTERATIONS
While you can’t control the weather, you can control the process, and nothing will derail a construction schedule faster than changes to the plans.
For example, if you suddenly decide that you want to add a few feet to one side of the house, it will impact the footer diameter, and any change to the footprint of the house will cause monumental delays to the schedule, including starting the permitting process over again. Plus, these delays will be compounded by contractor availability. The excavating crew your builder scheduled will now have to be put on hold, which pushes back the foundation crew, which pushes back the log/timber erection team, which pushes back the other trades and so on.
How to Avoid It:
Don’t rush through design. Once your floor plans have been drawn, carefully examine every aspect of them. Fully understand the size and space allocation of each room as well as the plan’s relationship to the land you’re going to build it on. Walk the plan with your contractor on site, and make any tweaks to the layout before you think of submitting it for permits.
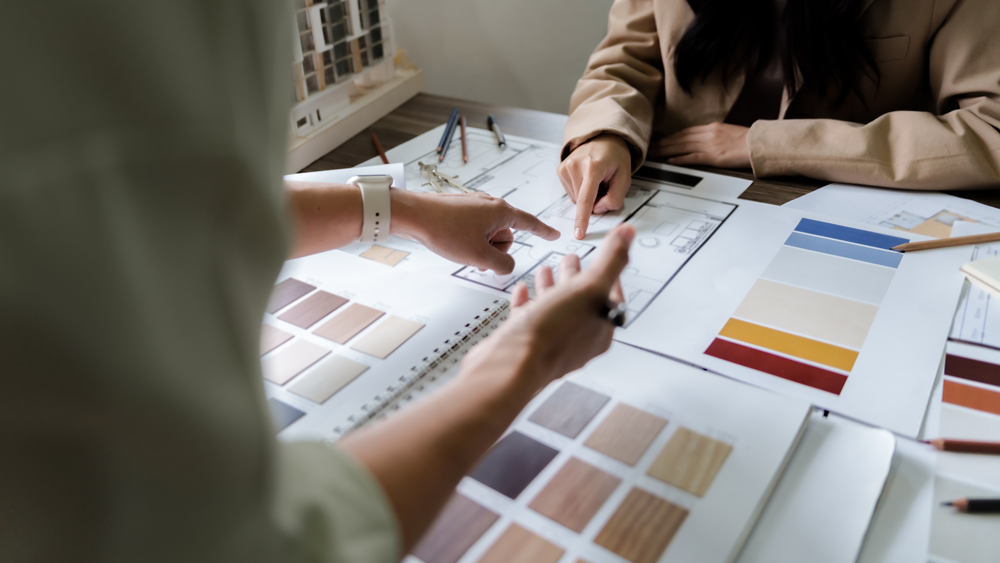
Cause of Delay: HOA RESTRICTIONS
Structurally your plans may be able to pass muster with the permitting office, but, if your property is governed by a homeowners’ association (HOA), it may not conform to their architectural guidelines. They can veto construction until you are compliant, which means redrawing the plans and submitting them for approval — to both the HOA and the permitting body— again. (You’d be surprised how many pieces of seemingly rural property are still overseen by an HOA.)
How to Avoid It:
Most HOA requirements are external and aesthetic, like the types of materials used to clad the exterior and setbacks from roads or features like lakes or forests; however, you still need to submit your design to them for approval. I recommend that you take this step before you take your plans to the permitting office. This way, you know you’re fully approved to build the home the municipality signs off on. Note: While the builder/contractor handles permits and approvals with the municipality, gaining the HOA’s OK is typically on you, the owner.
Cause of Delay: CHANGES
So, you’ve gotten your approvals, you’ve got your team in place and construction is moving right along. The number-one cause of delays at this point in the process is the client changing his or her mind. It doesn’t matter what it is … whether it’s the size of a room, the size of a window, the color of the stain or siding, the interior fit and finish … anything that you change your mind on has the potential to impact the schedule and cause delays. It has everything to do with the availability of materials and/or the trade contractors who will install it.
Here’s a real-world example that’s happening on a project I’m overseeing right now: My client is building a timber home and originally selected Nichiha siding in a “red cedar” look to clad the exterior. Recently she said she changed her mind, wanting a gray color instead. This is causing an eight-week delay. Why? It’s the same material, just a different color, right? Well, the red cedar is a standard option that’s readily available. Gray is a special-order shade. Furthermore, not only is the material going to take longer to obtain, the contractors may be committed to another job when it comes in, resulting in the potential for even more downtime.
How to Avoid It:
It’s simple. Before you sign off on any decisions — including finishing materials — make sure that’s what you really want. No matter how minor a deviation from the plan may seem, don’t change your mind.
See Also: A Typical Log Home Construction Schedule
Dan Mitchell is a log and timber home builder and educator, as well as president-elect of the Tennessee State Home Builders Association. He owns Eagle CDI, based near Knoxville.